EnfieldMotorcycles.in is the blog for all Royal Enfield enthusiast where we live, breathe, and eat Royal Enfield Bullet . We not only keep you informed of the news about Royal Enfield originals, but also give custom bikes and historical bikes a lot of attention. You can also find with us the best Enfield related movies and crazy stunts etc. We are testing and reviewing new models of which a complete relief will be shown on our site. Finally, we have technical tips, for example, how to properly get engine through the winter.
Read more
1. Removal of the Engine from the Frame
| ||||||||||||||
2. Removal of the Gearbox
Remove the primary chain case outer, clutch assembly, stator and rotor, engine sprocket and clutch sprocket. Remove the clutch centre and chain case inner.
Remove four 3/8" nuts and the gearbox can then be withdrawn from the engine. | ||||||||||||||
3. Dismantling the Crankcase
Drain the oil tank by removing the feed and return filter assembly plugs located in the crankcase bottom.
Having removed the engine from the frame dismantle the cylinder head, barrel, piston, timing gear etc., as described in the chapter "Decarbonising". Remove the nuts on the driving side of the engine from four fixed studs at the rear of the crankcase. Remove six studs passing through the crankcase by undoing nuts. The two halves of the crankcase can then be separated. The driving side outer race of bearings will remain in the driving side half of the crankcase. The driving side bearing inner race and the inner distance piece will remain on the engine shaft. ( Crankshaft) The flywheel assembly may be removed from the driving side of the crankcase. |
4. Removal and Reassembly of main bearings
Clean the crankcase thoroughly as any trace of oil in the crankcase will burn and discolour the bearing race while heating the crankcase.
Heat the crankcase in an oven or apply the naked flame of a blow lamp on the circumferential area of the bearing boss and not directly on the bearing race. When the crankcase gets heated up fairly, about 110º-120ºC, tap the crankcase on a wooden block (with the bearing race facing downwards) gently so that it will drop down due to the expansion of the bearing boss.
Remove the circlip from the driving side crankcase and reheat to remove the ball bearing.
Heat the crankcase in an oven or apply the naked flame of a blow lamp on the circumferential area of the bearing boss and not directly on the bearing race. When the crankcase gets heated up fairly, about 110º-120ºC, tap the crankcase on a wooden block (with the bearing race facing downwards) gently so that it will drop down due to the expansion of the bearing boss.
Remove the circlip from the driving side crankcase and reheat to remove the ball bearing.
Inspect the bearings before assembly. The bearing should spin smoothly. Rotated dry, it may appear to be slightly noisy but there should be no signs of corrosion, nor must there be any appreciable radial slackness. The outer race of the roller bearing must be preferably smooth and bright with no evidence of crack or pitting. The individual rollers must show no signs of wear and should rotate smoothly in the cage. It is recommended to replace with new bearings once they are removed from the crankcase.
Reheat the crankcases to reassemble the bearings in the crankcase. Assemble the ball bearings in the D/S crankcase after fitting the circlip. Locate the other circlip, distance tubes outer and inner and then assemble the roller bearing outer race.
Ensure that the bearings are seated properly in the crankcase and the outer roller race is flush with the crankcase.
Reheat the crankcases to reassemble the bearings in the crankcase. Assemble the ball bearings in the D/S crankcase after fitting the circlip. Locate the other circlip, distance tubes outer and inner and then assemble the roller bearing outer race.
Ensure that the bearings are seated properly in the crankcase and the outer roller race is flush with the crankcase.
Replacement of the Cam Idler Spindles
When wear is noticed or step formation seen on the spindle, it should be replaced. To remove the cam spindle, heat the crankcase and tap the spindles out from inside.
To remove the idler pinion spindles, heat the crankcases as before, hold the spindles in a vice and tap the crankcase lightly with a nylon/wooden hammer.
To replace the cam spindles, locate the spindles in respective holes in the timing side crankcase and drive the spindles in home with a small hammer (1/2 lb.) and a drift. Make sure that the spindles are upright and parallel to each other.
To remove the idler pinion spindles, heat the crankcases as before, hold the spindles in a vice and tap the crankcase lightly with a nylon/wooden hammer.
To replace the cam spindles, locate the spindles in respective holes in the timing side crankcase and drive the spindles in home with a small hammer (1/2 lb.) and a drift. Make sure that the spindles are upright and parallel to each other.
6. Connecting Rod
Wear in the hardened steel big end bush will be shown by a formation of a ridge round the centre of the bearing surface corresponding with the oil groove in the white metal floating bush. If this wear is excessive, the connecting rod should be replaced.
Excessive wear on the small end of the connecting rod can be easily seen. The Gudgeon Pin will show a rocking motion if wear is excessive.
Excessive wear on the small end of the connecting rod can be easily seen. The Gudgeon Pin will show a rocking motion if wear is excessive.
7. Flywheel Assembly
The flywheel assembly consists of the crankshaft and the connecting rod.
To dismantle the crankshaft remove the set screws securing the crankpin nuts. Holding the crankshaft in a special jig (PED 2037) remove the crankpin nuts.
Using PED 2037 with a pair of steel bars (about 1" x 3/8" x 9" long) placed across between the flywheel disc, press out the crankpin using a hand press.
The connecting rod can then be removed along with floating bush.
To dismantle the crankshaft remove the set screws securing the crankpin nuts. Holding the crankshaft in a special jig (PED 2037) remove the crankpin nuts.
Using PED 2037 with a pair of steel bars (about 1" x 3/8" x 9" long) placed across between the flywheel disc, press out the crankpin using a hand press.
The connecting rod can then be removed along with floating bush.
Turn the crankshaft over in the jig and repeat with other side if necessary.To remove the timing shaft, remove the set screw from the shaft nut and unscrew the nut. Drive the shaft out with a hammer and drift. To replace the timing side shaft, reverse the above process, making sure that the key is a good fit and that the nut is tightened securely by means of a box spanner with a 12" tommy bar.
The driving shaft has no nut but is secured by tightening the sprocket nut after the assembly of the engine. It should be pressed in with a hand press or a hammer and drift. If the latter is used, care must be taken not to damage the centre. It has a collar which butts against the flywheel disc.
To reassemble the crankshaft, press the crankpin into the timing side flywheel, making sure that the oil hole is in the correct position and the thrust washer is facing the right way, i.e. with Chamfer away from the flywheel.
To reassemble the crankshaft, press the crankpin into the timing side flywheel, making sure that the oil hole is in the correct position and the thrust washer is facing the right way, i.e. with Chamfer away from the flywheel.
Test the oil passages using an oil can to make sure that they are clear.
Assemble the floating bush over the crankpin.
Assemble the connecting rod over the floating bush and smear with engine oil.
Place the other thrust washer over the crankpin, also with the Chamfer away from the flywheel.
Use a brass drift and hammer for pressing the D/S flywheel.
Locate the flywheel in the assembly jig, to ensure that the flywheels and shafts are in line, and replace the nuts. Tighten securely and refit the set screws.
Assemble the floating bush over the crankpin.
Assemble the connecting rod over the floating bush and smear with engine oil.
Place the other thrust washer over the crankpin, also with the Chamfer away from the flywheel.
Use a brass drift and hammer for pressing the D/S flywheel.
Locate the flywheel in the assembly jig, to ensure that the flywheels and shafts are in line, and replace the nuts. Tighten securely and refit the set screws.
Test the oil passages again to ensure that they are clear.
If the same crankpin has been put back, it will be necessary to drill out the old grub screw in order to clean the oil passages after which a new grub screw must be fitted.
Mount the crankshaft between the centres of a lathe or on a pair of vee block and true up to 0.001" on either side of the shafts.
If the readings for the two shafts are high on opposite sides, the error can be corrected by gently tapping either or both of the flywheels.
If the readings are high on the same side of the two shafts, it is probably due to dirt or foreign matter in the joints and the crankshaft should be dismantled again, carefully examined and reassembled.
If the same crankpin has been put back, it will be necessary to drill out the old grub screw in order to clean the oil passages after which a new grub screw must be fitted.
Mount the crankshaft between the centres of a lathe or on a pair of vee block and true up to 0.001" on either side of the shafts.
If the readings for the two shafts are high on opposite sides, the error can be corrected by gently tapping either or both of the flywheels.
If the readings are high on the same side of the two shafts, it is probably due to dirt or foreign matter in the joints and the crankshaft should be dismantled again, carefully examined and reassembled.
8. Reassembly of the Crankcase
Replace the bearings, etc., in the crankcase halves after heating the crankcase as described earlier. (Refer page 29)
Fit the inner distance piece in the driving side crankcase.
Fit the thrust washer on the drive shaft. Fit the bearing inner race on the drive shaft. Assemble the flywheel into the bearing. If necessary use the sprocket nut with a suitable spacer to draw the driving shaft through the inner race of the ball bearing.
Make sure that the crankcase face is clean and apply jointing compound to it and fix the crankcase gasket in position.
Put the thrust washer on the timing side shaft and press the bearing inner race.
Bolt the two halves of the crankcase together making sure that the joint matches correctly so that the cylinder base is flat.
Rotate the drive shaft by hand and check for free rotation to ensure correctness in assembly and press the oil seal on to the drive side of the crankcase from outside, ensuring proper seating.
For 500cc
Press the oil seal onto the timing side of the crankcase and ensure proper seating
NOTE : Before attempting to remove the internal parts, please ensure that the clutch assembly has been dismantled along with F.D. sprocket.
Related Posts by categories
Show your Love for Royal Enfield !!
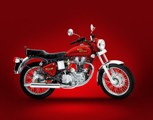
Cleaning your Royal Enfield
An exhaustive article about cleaning and maintaining your royal enfield !!

EFI Made Easy
Everything you need to know to take care of the system on your new EFI Royal Enfield in one short article.
Post a Comment